What if the industry considered end-of-life tyres (ELTs) as new commodities and not waste? The billion-plus tyres discarded annually can provide valuable secondary feedstock for tyre manufacturing, ushering in circularity in the automotive sector. Replacing virgin carbon materials with circular ones can significantly cut tyre companies’ footprints while manufacturers will be able to meet their ambitious 2050 goals of becoming net zero and increase the proportion of recycled and sustainable materials in their tyres.
Turning ELTs into recycled materials
The tyre-to-tyre model, where raw materials are sourced from ELTs, receives considerable attention and is one of the many available options, but tyre recycling is challenging. Tyres are tough and designed to resist water, temperature, ozone, and mechanical damage. They owe their durability and properties in part to composites, but composites are difficult to recycle and require novel technologies.
Another tricky aspect is the number of materials used in a tyre, such as natural and synthetic rubber, steel, textiles, and carbon black (CB). Steel is already often recycled in a closed loop to make new products. However, textiles recycling is more difficult because they are low-value materials and lack viable recycling methods.
Devulcanisation technologies to separate as many as 20 types of rubber are still being developed as it’s complicated. And mechanical recycling, the standard recycling process used to treat 87% of ELTs, retains the composite nature of tyres. Chemical recycling, proven to break down synthetic plastic polymers into component chemicals, shows great potential in delivering circular raw materials for the tyre industry. It can transform ELT recyclers into specific feedstock suppliers.
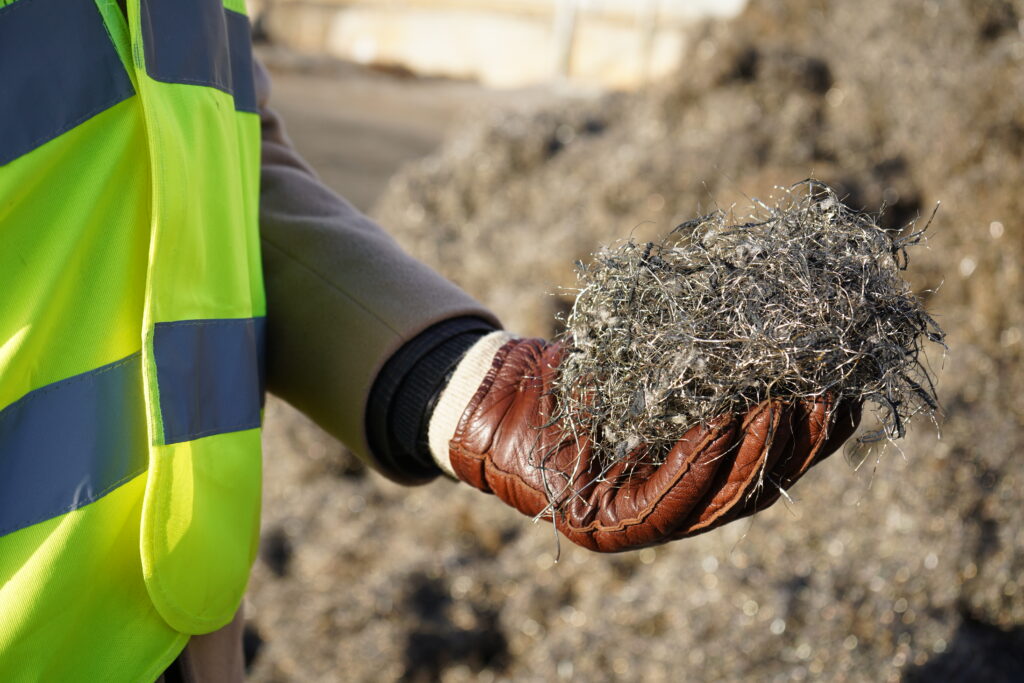
Designing more recyclable tyres
Considering circular and recyclable perspectives during the initial product design will enable more circular tyres in the future. Revaluating all the components of the tyre structure during this phase will proactively mitigate the revaluation problems that arise at the end of their life cycle. And increased attention to recycling in the design phase of tyres will bring higher volumes of circular, sustainable raw materials for the automotive industry.
Moreover, providing clear material information—like descriptive inscriptions on tyre sidewalls—can significantly aid the recycling process. This strategy results in several positive outcomes, including lowered energy consumption, decreased environmental pollution by minimising waste, a strengthened circular economy, and ensured sustainability of the tyre waste recovery processes.
Paving the future
Tyre pyrolysis is a standard chemcycling process, but market interest in the process is recent due to its potential contribution to a circular economy. The technology allows material recovery from waste rubber to yield raw materials like tyre pyrolysis oil (TPO), recovered gas, and recovered carbon black (rCB). Though 95% of materials from ELTs can be reused, due to the limited availability of pyrolysis technology, only a small portion of ELTs are even recycled to recover raw materials for the closed-loop tyre-to-tyre production model.
Adding novel methods like the Molten technology to tyre pyrolysis has significantly improved process safety. Molten technology brings unparalleled energy input control into the reactors, allowing complete control over process parameters. This adds stability, repeatability, and quality consistency.
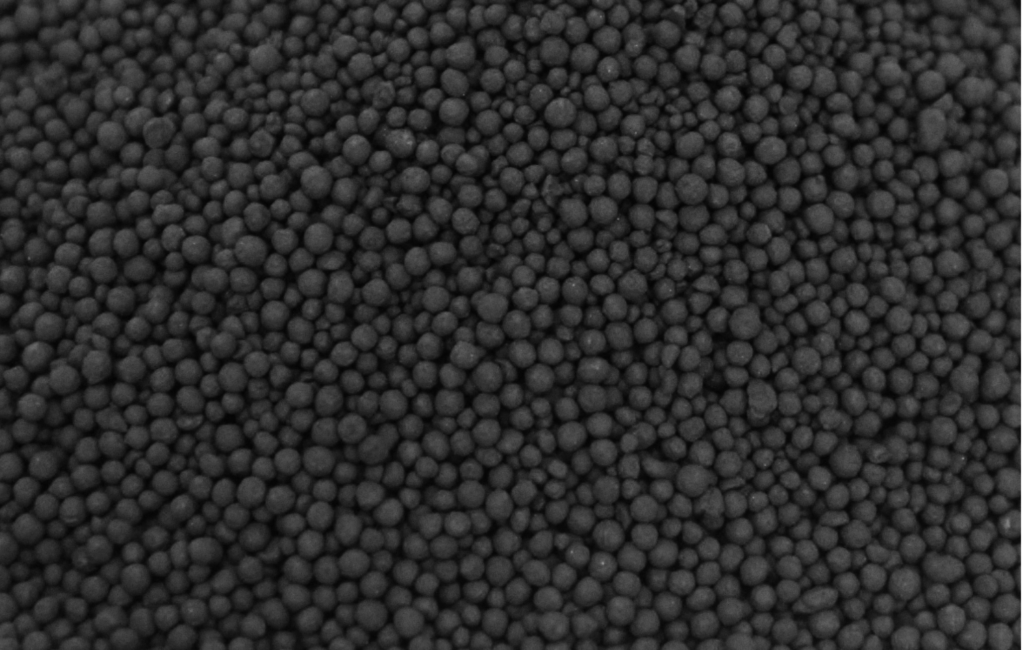
Faster recovered material adoption
Regardless of material sourcing, the common approach followed by tyre producers is forging partnerships to position themselves in the new circular value chain. Automotive industry stakeholders collaborating on asset management will benefit from sharing expertise, resources, infrastructure, and investments from joint research, technology development, and collective adoption of innovative solutions. Standardisation of rCB is one of these mandatory to scale up wider adoption.
For instance, Contec S.A. is one of the companies collaborating with the American Society for Testing and Materials (ASTM), a nonprofit organisation developing standards and analytical methods for materials through voluntary international consensus. ASTM gives the tyre industry stakeholders a forum to discuss and collaborate on the technical features of rCB. As the tyre pyrolysis industry is still growing, cooperation could prove more helpful than competition for the entire value chain. Collaboration between stakeholders along the value chain and among feedstock producers will likely be crucial to resolve issues in creating common standards and tests for rCB.
Shaping the future of mobility
By using circular products from ELTs, tyre manufacturers can significantly reduce their tyres’ carbon footprint and avoid the emissions and costs of conventional ELT waste management. Leading tyre manufacturers have begun using rCB and TPO-derived feedstocks to make their tyres sustainable. However, tyre manufacturers can achieve this reduction only by collaborating with partners.
In a circular business model, no individual tyre producer can address the interconnected challenges of reliable circular raw material supply, waste management, and environmental pollution. Cooperations can help partners deal with these challenges and stay ahead of their competition in the new circular automotive industry.
About the author: Krzysztof Wróblewski is Chief Executive Officer and Chief Technology Officer at Contec