Manufacturers play a crucial role in achieving a sustainable and environmentally friendly future. They have the power to directly influence resource usage through various measures such as reducing their reliance on new raw materials. Product design is also key in increasing circularity, as rethinking the design of many everyday items (like tyres) can help minimise waste.
Product design should incorporate more circular materials into manufacturing stages to promote material reuse and recycling, conserve natural resources, and limit energy use and carbon emissions. The tyre-to-tyre model closes the material loop in tyre production and reuses old tyre materials to make new tyres. End-of-life tyres (ELTs) are a valuable resource, and several technologies can be used to recover the materials as alternatives to standard virgin fossil fuels-based raw materials.
Given the complexity of tyre recycling, there are many ways that redesigning tyres can incorporate more circularity in the long run.
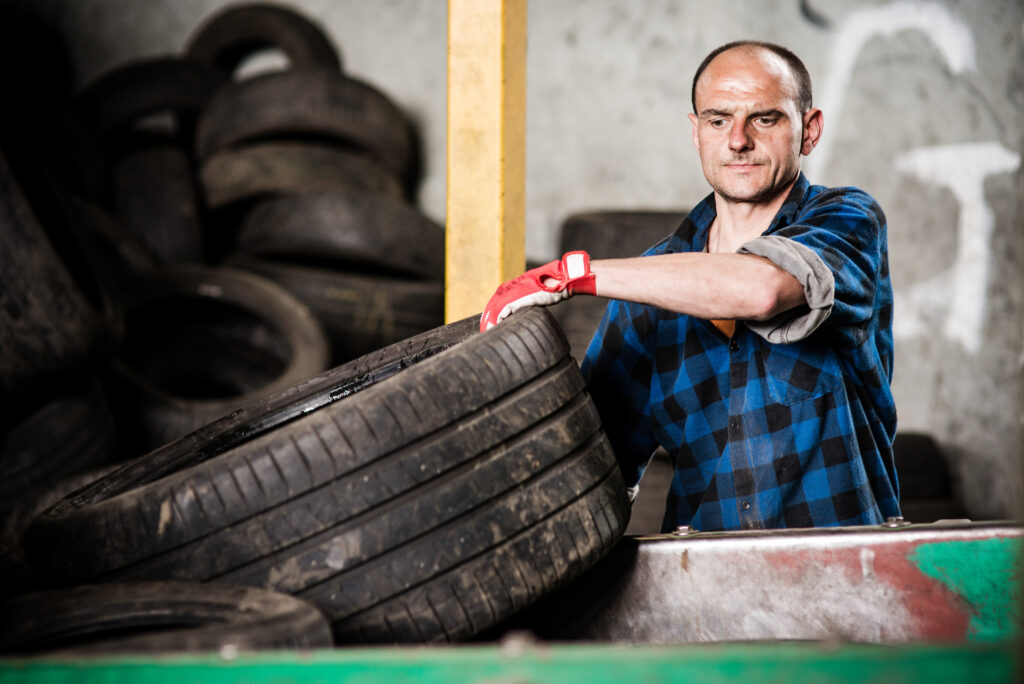
Materials and manufacturing
Tyres are made of rubber composites to improve performance. This makes recycling ELTs challenging. One way for suppliers to increase sustainability is to give up fossil-fuel-based raw materials like rubber and fillers, which create pollution and have a high carbon footprint. Instead, they can choose recycled secondary materials, like recovered Carbon Black (rCB) and Recovered Steel, that can be further recycled. Manufacturers can also use bio-based ingredients like rubber from dandelions instead of Hevea brasiliensis or fillers made from rape seed oil.
The choice of materials in the design stage is crucial in achieving circularity. Rubber elastomers, steel, and textiles used in tyres are integrated using adhesives, making subsequent disassembly difficult. Choosing additives and composites with specific rubber polymer types can simplify disassembly before recycling.
Circular materials like rCB, steel, and Tyre Pyrolysis Oil (TPO) can close the material loop in tyre manufacturing. These materials are produced from ELTs. Other components from ELTs, like rubber crumble, can also make new tyres. An industry-level effort and cooperation will be necessary to collect ELTs for recycling and reusing these materials in circularly designed automobiles.
Invest in modular design
Another significant benefit of circular design is the production of standard modular components. Product design can irreversibly affect the ease of separating components for later reuse and recycling, which causes circularity to involve considerable technology and energy. Component separation is a recycling challenge that reduces tyre material recycling, repurposing, and economic circulation. The difficulty of tyre disassembly means nearly 50% of ELTs are incinerated.
Manufacturers can invest in new innovative tyre designs that produce modular individual components for simpler disassembly for recycling, repair, and reuse in manufacturing new tyres. Similarly, modular components in new car designs will allow for more replacement and repair, decreasing demand for new vehicles and lessening the use of new raw materials to build cars.
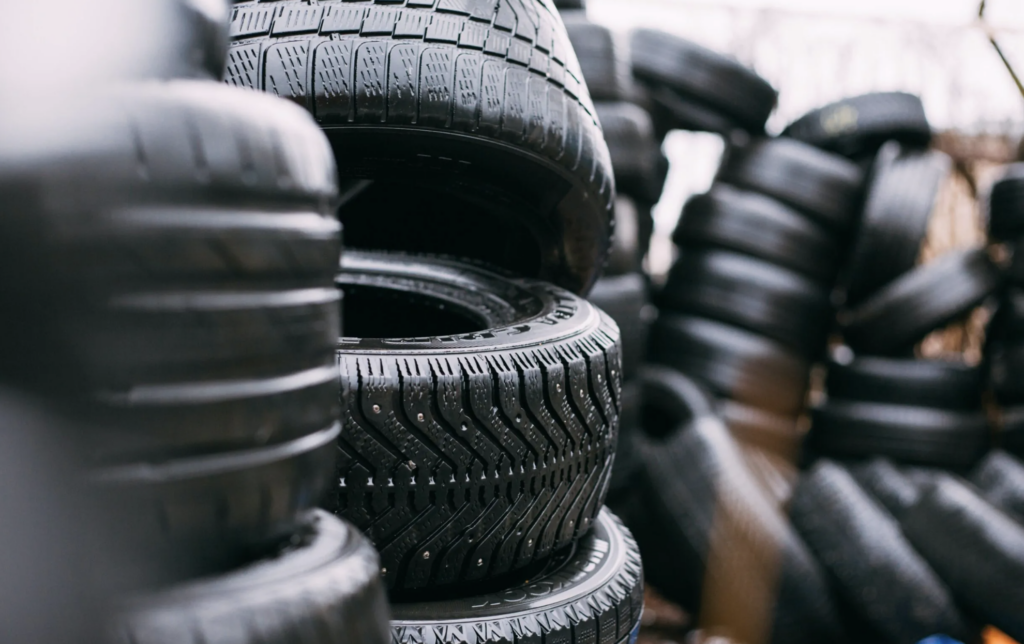
Recycling and reuse
An initial product design incorporating future recycling is necessary to keep tyre materials in circulation. The recycling process will need to be improved to allow for more efficient separation of materials and to increase the demand for recycling and reuse in new tyre manufacturing. Successful tyre redesign will consider the ELTs a valuable resource to produce secondary products, preventing them from being incinerated or landfilled.
Circularity in product redesign can enable automotive and tyre manufacturers to take responsibility for their products’ entire lifecycle, as stipulated by various regional Extended Producer Responsibility regulations. However, manufacturers must also take responsibility for other stages of the process by organising proper disposal and recycling of end-of-life products.
Governments can encourage circular design practices and the development of necessary technologies by passing regulations to support industries and incentivise circularity. For example, under the Extended Producer Responsibility policy, manufacturers in the EU must pay for the waste they generate.
The new EU Right to Repair policy proposed in 2023 should be another incentive for adopting circular and modular design practices in the automotive and tire industries.
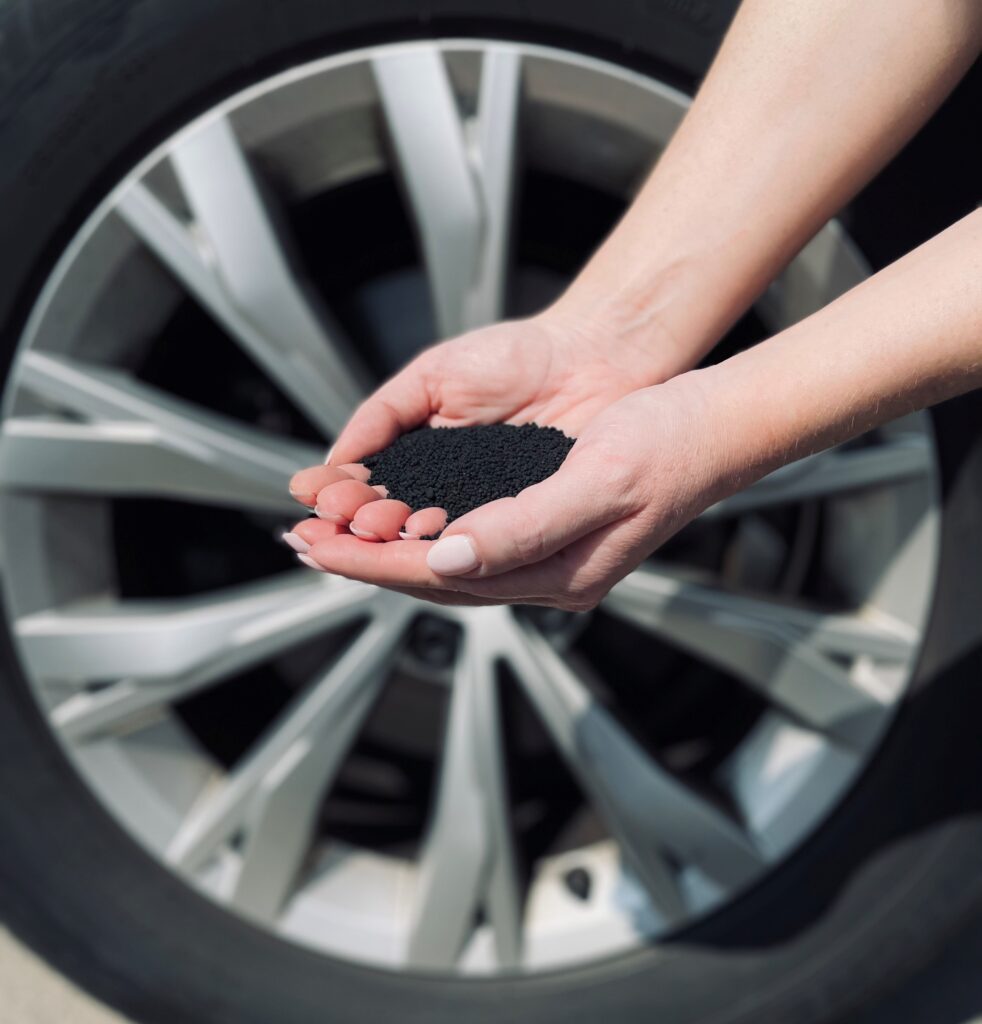
Designing for recycling
The tyre industry has been focused on developing and manufacturing fuel-efficient tyres to make sustainable and environmentally friendly cars. However, manufacturers can also aim to streamline recycling by integrating it into tyre designs to increase the use of circular, sustainable raw materials in the automotive industry.
Circularity in automotive and tyre product designs will also increase innovation, business opportunities, supply security, and industry cost savings.
The opinions expressed here are those of the author and do not necessarily reflect the positions of Automotive World Ltd.
Krzysztof Wróblewski is Chief Executive of Contec
The Automotive World Comment column is open to automotive industry decision makers and influencers. If you would like to contribute a Comment article, please contact editorial@automotiveworld.com