The IEA predicts that the world will have 300 million electric vehicles (EVs) on the road by 2050, accounting for more than 60% of new car sales, and up from just 10 million in sales today. The key to this growth—and for individual EV makers to distinguish themselves in an increasingly crowded market—is better battery technology.
EV manufacturers rely on maximised battery production rates to meet growing demand, but battery makers are struggling to keep up because they have diverse production needs, shortened project timelines and limits on their production capabilities. However, these challenges can be solved with a connected battery gigafactory. This requires deploying intelligent and effective manufacturing using digital visual support tools that can help reduce downtime, accelerate projects and allow for offline testing.
The foundation of a successful gigafactory
The cornerstone of any connected gigafactory is a manufacturing execution system (MES). MES provides real-time information about the production process, including data on materials, machines and personnel to help manufacturers optimise production planning and scheduling, monitor inventory levels and analyse production data to identify opportunities for improvement.
EV manufacturers rely on maximised battery production rates to meet growing demand, but battery makers are struggling to keep up
A MES is a crucial factor in enabling digitalised businesses to respond to market demands faster. One of the core functions of a MES is its ability to address lifecycle challenges in the digital world before they become “if only” moments in the real world. Additionally, MES supports exceptional agility and flexibility when combined with modelling and simulation tools to test “what if” scenarios offline. By connecting operations across plants and global business systems, MES enables production personnel to make faster and smarter decisions using real-time insights, resulting in expedited reaction times which, ultimately, saves time and money in the long run.
The role of digital twins in meeting demand
Meeting the challenges of shortened project timelines, improving production capabilities and changing production requirements requires EV manufacturers to use simulation software, like digital twins. A digital twin is more than just a visual representation of an asset or system; it’s a dynamic model that behaves and responds to conditions just as it would in a real world operational scenario.
Digital twins allow manufacturers to test scenarios offline, which in turn facilitates the continuous improvement of assets over their lifespan. With digital twins, it is possible for manufacturers to design, test and verify machines and plants long before they have to purchase parts or scale up their workforce. This capability can enhance the performance of workers and help EV manufacturers keep up with the rapidly evolving industry.
Digital twins in the design process
Manufacturers can use digital twins in three key areas during the gigafactory design process.
Demonstration
Digital twins give manufacturers the ability to create conceptual models of plants and analyse how the initial system design functions before ever starting production. From fitting a facility to solidifying a detailed production flow, digital twins provide workers with the tools they need to create a 3D layout of the conceptual model. This helps manufacturers develop a clear concept, which in turn can reduce development time and improve decision-making.
Testing
Once a manufacturer has received approval on their modelled concept, it can move on to the second step in launching a gigafactory: testing the design by simulating and experimenting with the digital twin. Crucial for manufacturers, testing allows them to make decisions about factors like equipment selection. For example, they may need to decide between cheaper equipment that processes slower or more expensive equipment that processes quicker. It is also important for a system to meet both current and future demands and testing can help manufacturers determine if the design will meet demand over time. Manufacturers can simulate these tests by configuring different variables and then running models at a pace that suits the specific needs of their factory.
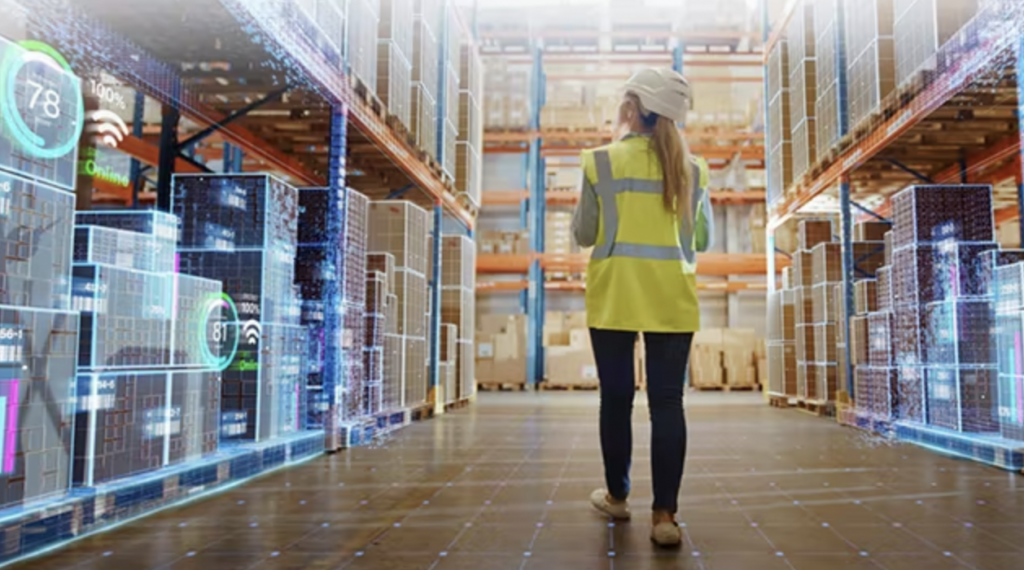
Emulation
The third area involves conducting offline testing of novel production processes. By leveraging emulation, engineers can execute their programmes in a virtual environment that includes 3D computer-aided design (CAD) objects to evaluate the entire system holistically without the need to construct the actual machine. They can create a virtual machine that employs genuine operational logic and interfaces with a control system. This enables manufacturers to examine, troubleshoot and confirm the machine’s performance before commissioning it, as well as emulate the machine to test new product types and configurations. Additionally, emulation lets manufacturers perform tasks that might be too hazardous, time-consuming and costly, consume excessive raw materials or jeopardise other production processes on the plant floor. This means manufacturers can digitally evaluate their systems with significantly less time, money and risk.
The electric vehicle (EV) revolution is well underway, and manufacturers need to design an infrastructure that can power the growing volume of EVs worldwide. Through digital twins, EV and battery manufacturers can build value across their operations, innovate digitally to meet demand and scale production.
About the author: Cliff Rice is Electric Vehicle and Battery Industry Consultant at Rockwell Automation